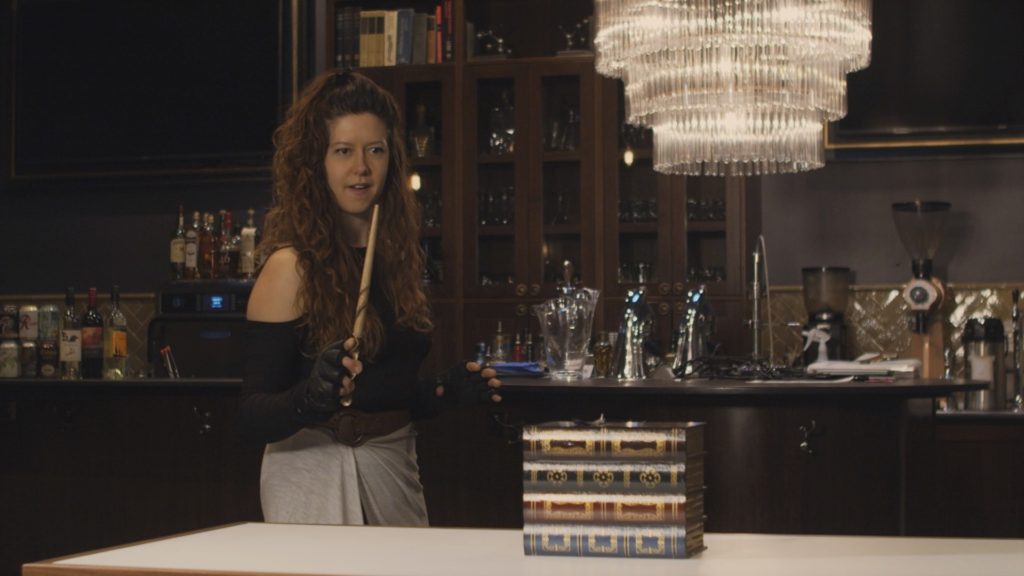
“Any sufficiently advanced technology is indistinguishable from magic.” (Arthur C. Clarke). Heck yes it is! What are we waiting for, let’s use technology to create our own kind of magic!! This project uses two micro:bit microcontrollers, a household cooling… Read more