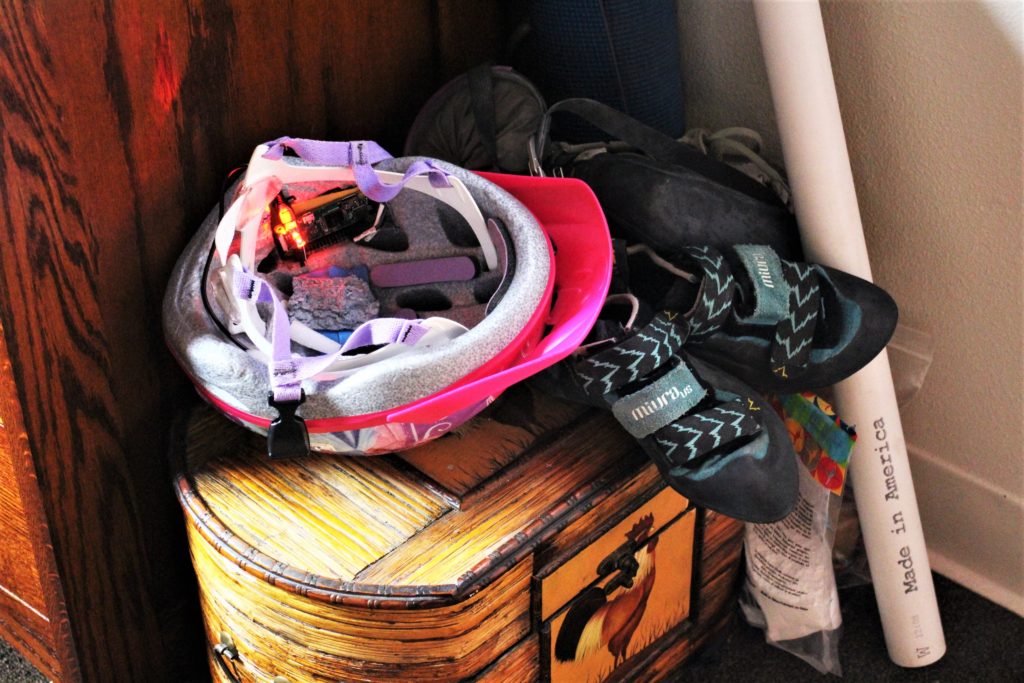
How much impact can the human body handle? Whether it’s football, rock climbing, or a bicycle accident, knowing when to seek immediate medical attention after a collision is incredibly important, especially if there are no obvious signs of trauma. This… Read more