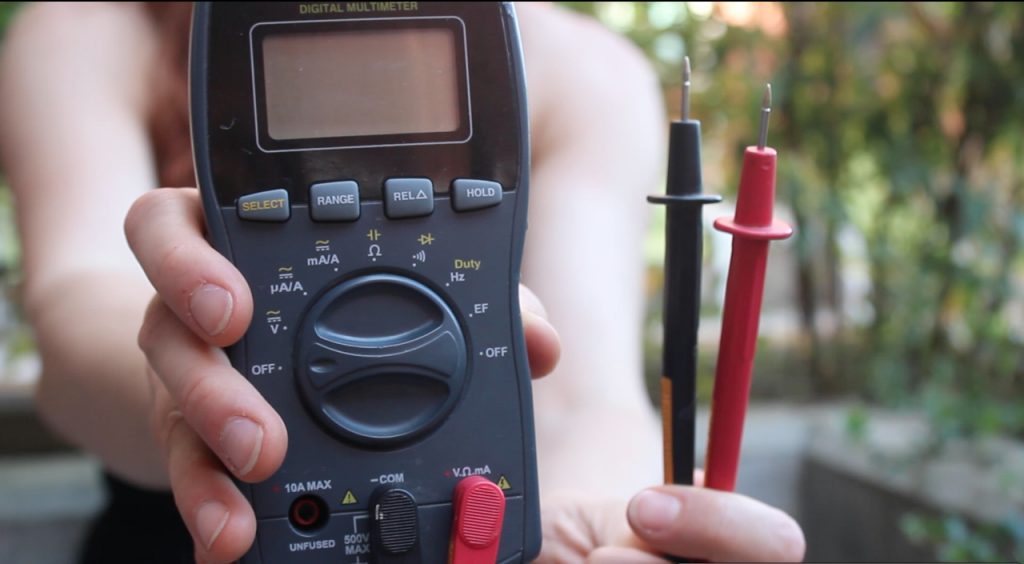
Checking your car battery life, debugging circuits, and finding that pesky short are all super useful functions that can be performed with just one awesome tool: the multimeter! First of all, what the heck is a multimeter?? Excellent setup question!… Read more